"When a hydraulic hose failed at a German steel plant last year, 12 tons of molten metal solidified in transfer lines – causing $2.3M in downtime. This preventable disaster underscores why understanding hydraulic hoses isn’t optional; it’s operational survival."
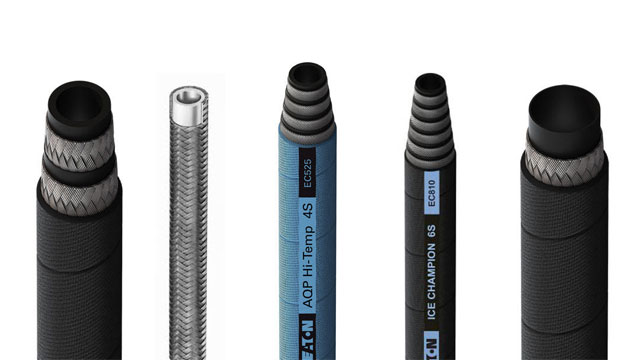
With over 70% of hydraulic system failures traced to hose and connector issues (Fluid Power Journal), this guide delivers the complete technical foundation for selecting, maintaining, and troubleshooting these critical components.
1. What Are Hydraulic Hoses?
Hydraulic hoses are flexible, reinforced conduits designed to transmit pressurized fluid between pumps, valves, cylinders, and actuators in hydraulic systems. Unlike rigid pipes, they accommodate vibration, movement, and complex routing while containing pressures exceeding 10,000 PSI.
Anatomy of a Hydraulic Hose:
l Inner Tube: Synthetic rubber (NBR, EPDM) or thermoplastic (PTFE) compatible with hydraulic fluids
l Reinforcement Layer: High-tensile steel wire braids (2-6 layers) or spirals
l Outer Cover: Abrasion-resistant synthetic rubber (CR, CSM) with additives for UV/ozone resistance
l End Fittings: Crimped or screwed connectors (JIC, NPT, BSPP)
Critical Function: They transform fluid power into mechanical force while absorbing system shocks that would damage rigid components.
2. How Hydraulic Hoses Work: Physics & Mechanics
Hydraulic hoses operate on Pascal’s Law: Pressure applied to confined fluid transmits equally in all directions. Here’s the physics in action:
1.Power Transmission:
l Pump pressurizes fluid (e.g., 46-grade mineral oil)
l Fluid enters hose at 3,000PSI → transfers energy to actuator
l Force = Pressure × Area (e.g., 3,000 PSI × 2 in² = 6,000 lbs force)
- Flow Dynamics:
l Flow rate (GPM) determines hose ID requirements
l Rule: Maintain 7-15 ft/sec velocity to prevent turbulence
l Pressure drop = (0.3208 × Q × L × μ) / (ID4)
(Q=flow, L=hose length, μ=viscosity, ID=inner diameter)
3.Bend Radius Science:
l Minimum bend radius = 4 × hose OD (standard)
l Exceeding bends causes wire reinforcement fatigue → premature failure
3. Types of Hydraulic Hoses (SAE/DIN Standards)
Type
|
Standard
|
Pressure
|
Layers
|
Best For
|
Wire Braid
|
SAE 100R1AT
|
3,000 PSI
|
1-2 braids
|
Tractors, forklifts
|
Wire Spiral
|
SAE 100R12
|
6,000 PSI
|
4-6 spirals
|
Excavators, presses
|
Thermoplastic
|
SAE 100R5
|
5,000 PSI
|
Aramid fiber
|
Food/pharma applications
|
PTFE/Teflon®
|
SAE 100R7
|
3,000 PSI
|
None
|
High-temp (400°F+), fuels
|
Coiled
|
SAE 100R16
|
1,500 PSI
|
1 braid
|
Robotics, tool changers
|
Specialty Variants:
l Conductive Hoses: Carbon-black covers dissipate static (ATEX Zone 1)
l Multi-Spiral Hoses: SAE 100R17 for 10,000+ PSI (offshore drilling)
4. Selecting the Right Hose: 7 Critical Factors
1.Pressure Rating:
l Working Pressure ≥ 1.25 × system max pressure
l Burst Pressure ≥ 4:1 safety factor (OSHA 1910.261)
2.Fluid Compatibility:
l NBR tubes for petroleum oils; FKM for phosphate esters
l Test: 70°C immersion for 1,008 hrs (SAE J517)
3.Temperature Range:
l Standard hoses: -40°F to 212°F
l High-temp: PTFE (-65°F to 500°F)
4.Bend Radius:
l Minimum radius = 4 × OD (e.g., 1" OD hose → 4" radius)
5.Environment:
l Abrasion: Use covers with M-Scale rating (MSHA 30A)
l Chemicals: EPDM covers resist oils/solvents
6.Size (ID):
l Calculate ID using: ID (in) = √(GPM × 0.3208 / Velocity)
7.Certifications:
l SAE J517 (US), EN 853 (EU), ISO 18752 (Int'l)
Recommended Hydraulic Hose Brands
Based on application-specific strengths:
Brand
|
Key Strengths
|
Typical Applications
|
Tech Edge
|
Parker
|
High-impulse resistance (4–6 wire spirals)
|
Excavators, presses
|
Cold-bend tech (-40°F flexibility)
|
Gates
|
MSHA-certified abrasion covers
|
Mining, construction
|
Ultraflex™ low-force bending
|
TRELLEBORG
|
PTFE liners for chemicals/fuels
|
Chemical processing
|
Zero-permeation technology
|
ULTPRE
|
High-temp PTFE (500°F+), nano-reinforced covers
|
Steel mills, foundries
|
NanoShield™ abrasion resistance
|
TITANTUBING
|
Cost-effective SAE 100R4/R12
|
Agriculture, utilities
|
Steel-wire anti-kink spirals
|
Why ULTPRE? Their focus on extreme-temperature stability and nano-composite materials solves leakage/erosion in high-heat industries – a niche often overlooked by mainstream brands.
5. Hydraulic Hose Testing & Inspection Protocols
Destructive Tests:
l Burst Test: Ramp pressure to 4× WP → record failure point
l Impulse Test: Cycle between 0-133% WP until failure (SAE J343)
Non-Destructive Tests:
l Ultrasonic Thickness Gauge: Detects ≥0.1mm wall thinning
l Vacuum Testing: Apply 25" Hg vacuum → check for cover collapse
l Proof Testing: Hold at 1.5× WP for 3 mins (annual requirement)
Visual Inspection Checklist:
l Cracks: >2 cracks per inch = replace
l Abrasion: >10% cover depth worn
l Kinks: Permanent deformation
l Bulges: Indicates broken reinforcement wires
6. Hydraulic Hose Lifespan: Real-World Data
Application
|
Avg. Lifespan
|
Failure Accelerators
|
Mobile Equipment
|
2-4 years
|
UV exposure, flex cycles
|
Industrial Machinery
|
5-8 years
|
Heat >200°F, contamination
|
Offshore Rigs
|
1-3 years
|
Saltwater, constant vibration
|
Lifespan Equation:
Service Life (hrs) = L0 × (P0/P)³ × (T0/T)¹°
(L0=rated life, P0=rated pressure, T0=rated temp)
Example: A hose at 120% WP and 250°F lasts just 12% of its rated life!
7. 6 Signs Your Hydraulic Hose is Failing
1.External Cracks: Ozone attack (check near fittings)
2.Weeping Fluid: Pinholed inner tube
3.Bulging/Blistering: Delamination of layers
4.Stiffness: Hardening from heat/chemical exposure
5.Discolored Fluid: Black particles = inner tube erosion
6.System Issues: Erratic cylinder movement, overheating
8. When to Replace Hydraulic Hoses
Replace immediately if:
l Exceeding manufacturer’s service life
l Visible steel reinforcement (wire exposure)
l Fitting corrosion >30% of diameter
l Permanent kinks or twists
Proactive Replacement Intervals:
l Critical systems: 75% of rated service hours
l High-vibration zones: 2 years max
9. Common Hydraulic Hose Defects & Root Causes
Defect
|
Cause
|
Solution
|
Inner Tube Erosion
|
High-velocity flow + particles
|
Install 10μ filters
|
Wire Corrosion
|
Water ingress (>500 ppm)
|
Use desiccant breathers
|
Cover Cracking
|
Ozone exposure
|
Store away from electric motors
|
Fitting Leaks
|
Improper crimp die selection
|
Calibrate crimpers monthly
|
10. Stopping Hydraulic Hose Leaks
Temporary Fixes (24-hour max):
l Emergency Clamp: Tridon Z77 clamp @ 50% pressure
l Sealant Paste: Henkel Loctite 565 on SAE threads
Permanent Solutions:
l Depressurize system → purge fluid
l Cut damaged section with rotary cutter (no burrs)
l Install reusable fittings (e.g., Gates Spin-Loc)
l Pressure test to 1.5× WP
Leak Prevention:
l Torque fittings to spec (e.g., JIC -12: 120 ft-lbs)
l Install protective sleeves (Aeroquip Fireguard)
11. Consequences of Hydraulic Hose Failure
Safety Hazards:
l Fluid Injection: 200 PSI penetrates skin → amputation risk
l Fire: Atomized oil ignites at 700°F (common near engines)
l Whipping Hoses: Unrestrained ends strike at 600 mph
Operational Impacts:
l Downtime costs: $10k+/hour in mining/oil
l Environmental fines: $50k+ for 50-gallon oil spills (EPA)
12. Repairing Hydraulic Hoses: Professional Protocols
SAE-Compliant Repair Steps:
1.Cut: Use abrasive wheel cutter (clean, square cut)
2.Skive: Remove cover to expose reinforcement
3.Measure: Insertion depth = 1.5 × hose OD
4.Crimp: Apply calibrated die (tolerance: ±0.004")
5.Test: Proof test @ 1.5× WP for 60 secs
When NOT to Repair:
l PTFE hoses (discard if damaged)
l 10% length compromised
l ritical safety systems (use new assemblies)
13. Conclusion: Proactive Hydraulic Hose Management
"Treat hydraulic hoses like aircraft tires – replace on condition, not failure."
Action Plan:
l Log Tracking: Record installation dates, hours, pressures
l Training: Certify staff in SAE J1273 inspection standards
l Partnership: Use ISO 9001-certified hose shops for assemblies
Final Warning: A $200 hydraulic hose failure can destroy a $250,000 pump. Spec wisely, inspect religiously.