By Girish Linganna
Jun 11:The Indian Space Research Organisation (ISRO) is preparing to conduct the third and final landing test for its Reusable Launch Vehicle (RLV) programme. This is a significant step towards making the RLV a reality. It is planned to carry out the test in first-half June at the Aeronautical Test Range in Chitradurga, Karnataka, although it would depend upon the weather conditions.
Vikram Sarabhai Space Centre (VSSC) Director Dr S Unnikrishnan Nair told the media that a Mission Readiness Review (MRR) carried out on Friday (June 7) had given the go-ahead for the forthcoming test mission. With this mission, the aim was to gradually increase the challenge, Dr Nair said, indicating the increasing complexity of the tests.
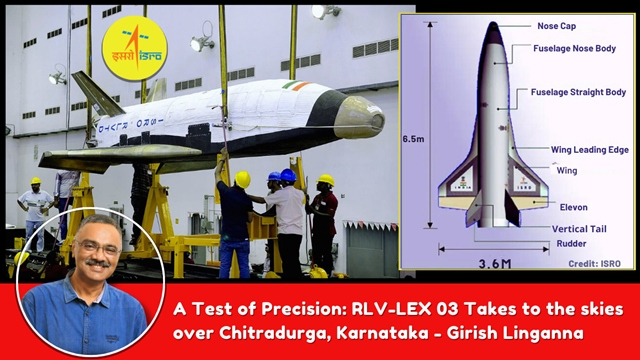
The RLV-LEX (Landing Experiment) missions involve using an unmanned winged prototype, called Pushpak. The Thumba-based VSSC was responsible for designing and developing Pushpak. During these missions, Pushpak is taken to a certain height and then released to land safely under different conditions. This helps test—and improve—its landing capabilities.
ISRO’s LEX-01 mission (April 2, 2023) and LEX-02 mission (March 22, 2024) went off like a dream.
In the forthcoming LEX-03 (Landing Experiment-03) mission, the 21-foot-long Pushpak will be airlifted by a Chinook to a height of 4.5 kilometres. But, this time, there will be an extra challenge. It will be released 500 metres away from the runway. In the LEX-02 mission, it was only 150 metres away. Pushpak would have to guide itself to the runway, adjusting its position and altitude to land safely, explained Dr Nair.
LEX-03 has a specific goal of decreasing the speed at which the aircraft descends during landing in order to minimize the impact force. To achieve this, the team will utilize a real-time kinematics (RTK) package to improve accuracy. In addition, they will tackle the challenge of landing in tailwind conditions.
After the LEX programme achieves success, ISRO’s RLV-TD project will go another step forward and use an unmanned Orbital Re-entry Vehicle (ORV). This is a larger vehicle—approximately 1.6 times Pushpak’s size—and will be launched into a 400-km orbit using a modified Geosynchronous Satellite Launch Vehicle (GSLV). This mission is expected to take place within the next two years.
The ORV mission will include different experiments conducted in space. These experiments will focus on testing a protective system against high temperatures when re-entering Earth’s atmosphere, as well as a landing gear system that can be folded away.
Advancing Reusability:
The RLV-TD Programme
The Reusable Launch Vehicle-Technology Demonstration Programme is a collection of missions initiated by ISRO to showcase and test various technologies. It serves as a preliminary step towards developing a fully reusable launch vehicle with two stages, where the second stage functions as a spaceplane. The goal is to create a cost-effective and efficient means of launching payloads into space, with the ability to reuse certain components of the vehicle.
To achieve this objective, ISRO has developed a winged reusable launch vehicle technology demonstrator (RLV-TD). This vehicle acts as a flying testbed to evaluate different technologies, including:
- Hypersonic aero-thermodynamic characterization of wing body: This term refers to studying how a wing combined with a body behaves in extremely fast supersonic flight. It involves understanding the effects of air and heat on the wing and body structure during high-speed travel
- Evaluation of autonomous Navigation, Guidance and Control (NGC) schemes: This means testing and assessing systems that let vehicles or aircraft navigate, make decisions and control themselves without human help. It checks if these systems work reliably
- Integrated Flight Management: This is a system that efficiently manages all aspects of a flight—including planning, navigation and performance. It enhances safety, fuel efficiency and overall flight operations
- Thermal Protection System Evaluation: This term refers to the assessment of materials and techniques used to protect spacecraft, such as space shuttles, from the extreme heat generated during re-entry into Earth’s atmosphere. It ensures the reliability and effectiveness of the protective systems against thermal stress
The successful application of these advanced technologies has the potential to significantly reduce the cost of launching payloads into space, potentially making it 10 times more cost-effective.
It All Began in 2012
Pushpak, which means ‘Flower’ in Sanskrit and is named after the Pushpaka Vimana, is an uncrewed flying testbed created for ISRO’s RLV Technology Demonstration Programme that began in 2012. It serves as a reduced-scale prototype for a future two-stage-to-orbit reusable launch vehicle.
In January 2012, ISRO got the go-ahead for the construction of its reusable launch vehicle from the National Review Committee. This vehicle was given the name ‘Reusable Launch Vehicle-Technology Demonstrator’ (RLV-TD). The primary goal of ISRO is to significantly reduce the cost of delivering payloads to low-Earth orbit (LEO) by 80%, aiming to bring it down from the current rate of $20,000 per kilogram to $4,000 per kilogram.
ISRO has scheduled a series of four test flights for RLV-TD:
o Hypersonic Flight Experiment (HEX)
o Landing Experiment (LEX)
o Return Flight Experiment (REX), later renamed Orbital Return Flight Experiment (OREX)
o Scramjet Propulsion Experiment (SPEX)
A 750-member team of dedicated engineers from the VSSC, National Aeronautical Laboratory and the Indian Institute of Science (IISc.) came together to design and develop the RLV-TD and its associated rocket. The process involved extensive testing, including 120 hours of wind tunnel experiments, 5,000 hours of computational fluid dynamics analysis and 1,100 flight simulation tests.
The RLV-TD has a mass of 1.75 tons and is 6.5 metres long. It has a wingspan of 3.6 metres, which is not inclusive of the rocket. It carries 600 heat-resistant tiles on its undercarriage and is fitted with delta wings and angled tail fins. The project had a total cost of ?95 crore (equivalent to ?137 crore, or US$16.4 million in 2023).
For future developments, ISRO plans to test an air-breathing propulsion system that harnesses atmospheric oxygen instead of relying solely on liquefied oxygen during flight. This innovation has the potential to further improve the efficiency of the launch vehicle.
(The author of this article is a Defence, Aerospace & Political Analyst based in Bengaluru. He is also Director of ADD Engineering Components, India, Pvt. Ltd, a subsidiary of ADD Engineering GmbH, Germany. You can reach him at: girishlinganna@gmail.com)