May 31, 2023
IT HAS ALWAYS BEEN DIFFICULT to get rid of old tyres. More than a billion of them reach the end of the road every year. Most of them are thrown in garbage dumps or piled up in storage yards, where they sometimes catch fire. Many countries now require that tyres be recovered because environmental laws have become stricter. And they kind of are. Some of the ways may be better than just throwing them away, but these aren’t very environment-friendly.
One such way is energy recovery. This entails burning tyres in an incinerator to create power or as a supplemental fuel for cement kilns and other industrial activities. However, this causes global warming and high levels of pollution. Tyres can be utilized whole, or shredded, in building operations, such as embankment construction or road repairs. However, there are concerns that chemicals from the tyres would bleed out and contaminate the earth.
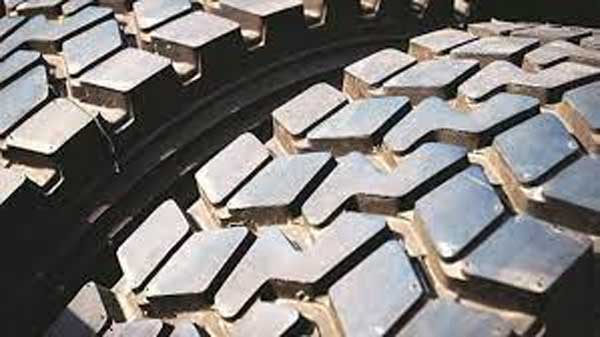
As a result, some businesses have started looking into a different, more symmetrical, option. Since hydrocarbons make up the bulk of a tyre’s composition, in theory, it should be able to convert worn tyres into low-carbon fuel that can power the vehicles they originated from.
Wastefront, a business established in Oslo, Norway, is one of the most ambitious organizations exploring the concept. A sizable tyre recycling facility will be built by the corporation in Sunderland, northeastern England, later this year. When the factory is fully operating in a couple of years, it will be able to convert 8 million old tyres into new goods, including about 25,000 tons of a sticky, black liquid known as Tyre-Derived Oil (TDO).
HOW TYRE DECONSTRUCTION WORKS
THE METHOD WORKS by disassembling a tyre into its three primary components. Steel, for instance, is used to support the structure of a tyre and is easily recycled. The second is carbon black, a powdered, soot-like carbon used to increase tyre durability. The third material is rubber. Some of it will be natural rubber derived from rubber tree sap. Some will be synthetic, produced in factories from crude oil.
To begin the deconstruction, the tyres are shredded and the steel bracing is removed. The leftover material is then subjected to a process known as pyrolysis. This is accomplished by subjecting a substance to high temperatures in the absence of air. As a result, the rubber decomposes into a mixture of hydrocarbon gases, which are then extracted. What remains is pure carbon black.
When the drawn-off gas cools, a portion of it liquefies into TDO. The residual gases, which include methane, are re-circulated and burned to power the reactor. According to Vianney Valès, Wastefront’s CEO, this provides a closed-loop system that eliminates pollutants. By weight, the process produces 40% TDO, 30% carbon black, 20% steel and 10% gas.
RECYCLING CARBON BLACK TIME & AGAIN
CARBON BLACK CAN BE USED over and over again to make new tyres. That’s important to people who make tyres because it helps them become carbon neutral. In order to make new carbon black, one has to partially burn heavy oil leftovers or coal, which gives off a lot of greenhouse gases.
TDO that has been collected is like crude oil that has just come out of the ground. It can be used to make diesel. Wastefront partners with Swiss company Vitol, the world’s biggest independent oil trader that runs refineries worldwide.
While not totally carbon-neutral, diesel derived from TDO emits 80%-90% less carbon dioxide, the principal greenhouse gas, compared to conventional fuel. Even as electric vehicles gradually replace those powered by combustion engines, the future market for cleaner fuels is expected to remain significant. Fossil-fuelled cars will continue on the roads for decades, particularly large commercial vehicles, such as lorries, which are difficult to electrify and are heavy diesel users. Trains and ships will also require fuel. So, anything that helps reduce total emissions throughout the protracted transition to electrification of transport is beneficial—especially if it also helps reduce a mountainous waste problem.