New Delhi, Sep 11 (IANS): Indian researchers have fabricated a paper honeycomb and stronger polymer honeycomb-structured sound-absorbing panels that dissipate acoustic energy to low-frequency ranges, and the technology can be used in building acoustics and also as environmental noise control solution, an official statement said on Friday.
Many traditional materials have been found to be good at controlling higher frequencies, but natural beehives have been found to efficiently control high as well as low frequencies because of their geometry, the Science and Technology Ministry statement said.
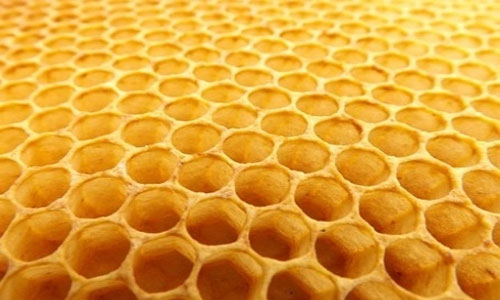
"It has been found from theoretical analysis and experimental investigations that this behaviour was owing to the conversion of acoustical energy into vibration energy. This vibration energy is dissipated in the form of heat due to wall damping property. Mimicking this property as an engineering solution could offer a cost-effective method for controlling noise pollution," it said.
Faculties at IIT Hyderabad's Mechanical and Aerospace Engineering Department, Dr B. Venkatesham and Dr Surya, fabricated low thickness and strong acoustic panels mimicking this property using biomimetic design methodology. The team also developed a mathematical model and calculated optimised parameters, and then fabricated the test samples using systematic, controlled parameters. Subsequently, fabrication of a large sample was done.
They have used two different approaches and their respective prototype machines with two different kinds of materials. One prototype is for paper honeycomb based on indexed Honeycomb Before Expansion process, and another prototype machine is for polymer honeycomb structure, based on hot wire technique.
The panels were made by slicing stacked extruded polypropene straws, with the help of hot wire, which also bonds the straws together. The developed technology provides a mechanism of acoustic energy dissipation with lower thickness and higher specific strength of acoustic panels. A test facility to measure the absorption coefficient of large samples was also established as part of this work.
This technology, supported by the Department of Science and Technology's Advanced Manufacturing Technologies programme is in the 6th stage of Technology Readiness Level, and Dr Venkatesham has allied with Eaton Pvt Ltd, the Maharashtra Industrial Development Corporation, Kharadi Knowledge Park, Pune, the release said.
He plans to further scale up the technology demonstration, develop a batch production machine for polymer materials, fabricate newer alternative self-damping materials, and comply with other safety requirements like flame retarding capacities, weather ability and so on.
Venkatesham said it may create an opportunity to capture 15 per cent of the traditional sound-absorbing acoustic material market based on the low-frequency applications, the release added.